Computer Numerical Control (CNC) machining is a subtractive manufacturing process that enables manufacturers to accurately and cost-effectively create high-precision parts. CNC machining removes excess raw material from workpieces with cutting tools to create a precise finished product from materials like plastic, metal, and composites.
These days, product teams have lots of options when it comes to multi-axis machining, from 3-axis to 5-axis to even 9-axis machining. What’s the difference between each type? In this article, we’ll break down the key similarities and differences between two popular types of CNC machining (3-axis vs. 5-axis) — and explain when it might make sense to use one over the other.
What Is 3-Axis Machining?
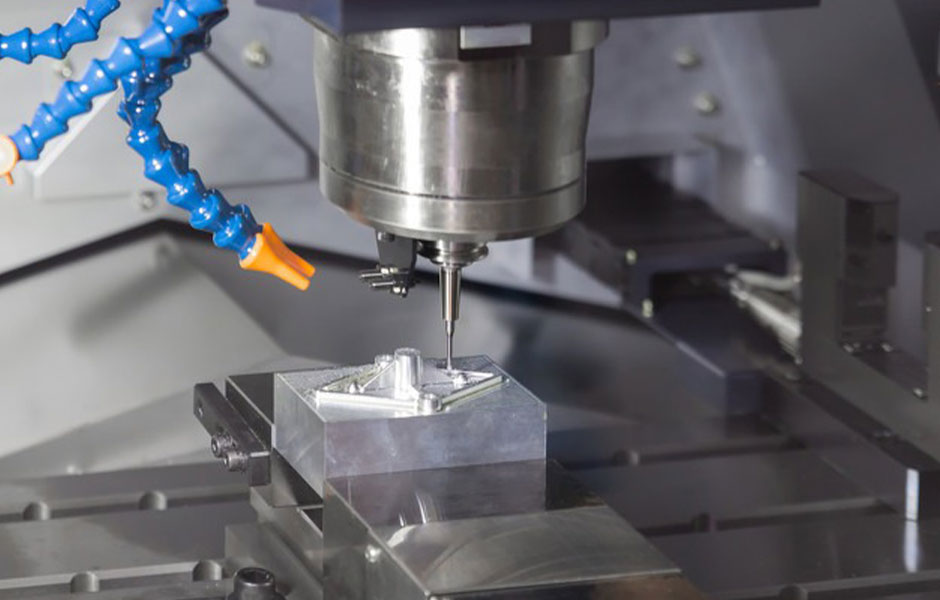
3-axis milling evolved from the practice of rotary filing and is a milling process that operated on two axes, the X & Y axis. In three-axis machining, the workpiece remains still while the cutting tool moves along the 3 axes to mill the part. 3-axis machining is still one of the most widely used techniques to create mechanical parts and can be used for automatic/interactive operation, milling slots, drilling holes, and cutting sharp edges. Because 3-axis machining only operates on the 3 axes, it’s relatively simple and allows the material to be removed in these 3 axes represented by back to front, side to side, and up and down.
While it is a more basic machining process, 3-axis machining may be ideal for your machining project depending on the size of your production run, the workpiece requirements, accuracy and finish constraints, materials used, and your holding capabilities.
What Is 4-Axis Machining?
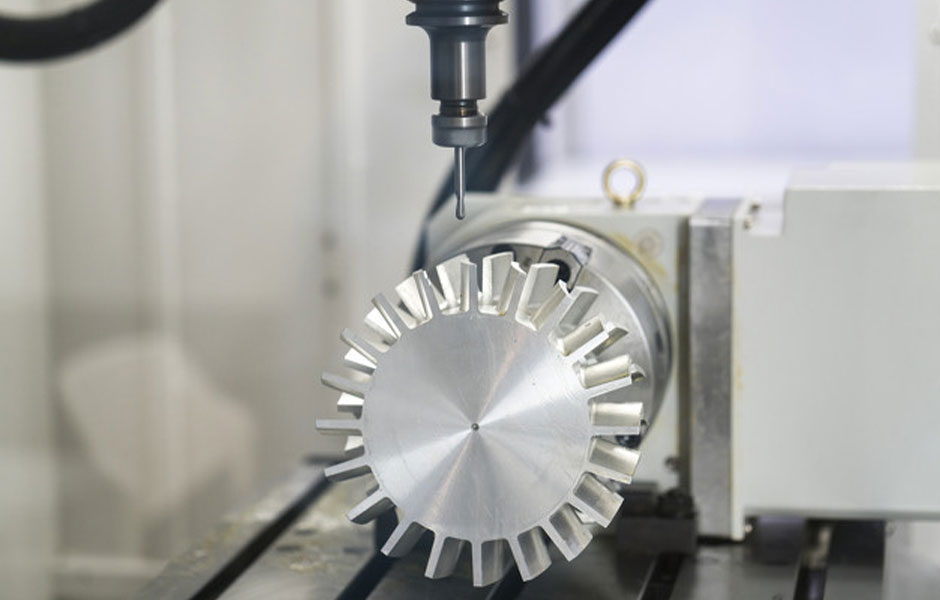
4-axis milling involves the same processes involved in 3-axis machining, where a cutting tool is used to remove material from a piece to create the desired shape and profile. However, in the case of 4-axes machining, milling is performed on an additional axis. A 4-axis CNC machine operates on the X, Y, and Z axes like a 3-axis machine, but it also includes rotation around the X-axis, which is called the A-axis. This is the 4th axis that’s added to our machining process. In most cases, the workpiece will be rotated to allow for cutting to occur around the B-axis.
4-axis milling is useful when holes and cut-outs need to be made on the side of a piece or around a cylinder. They can provide quick and efficient work based on computer numerical inputs for precise results.
What Is 5-Axis Machining?
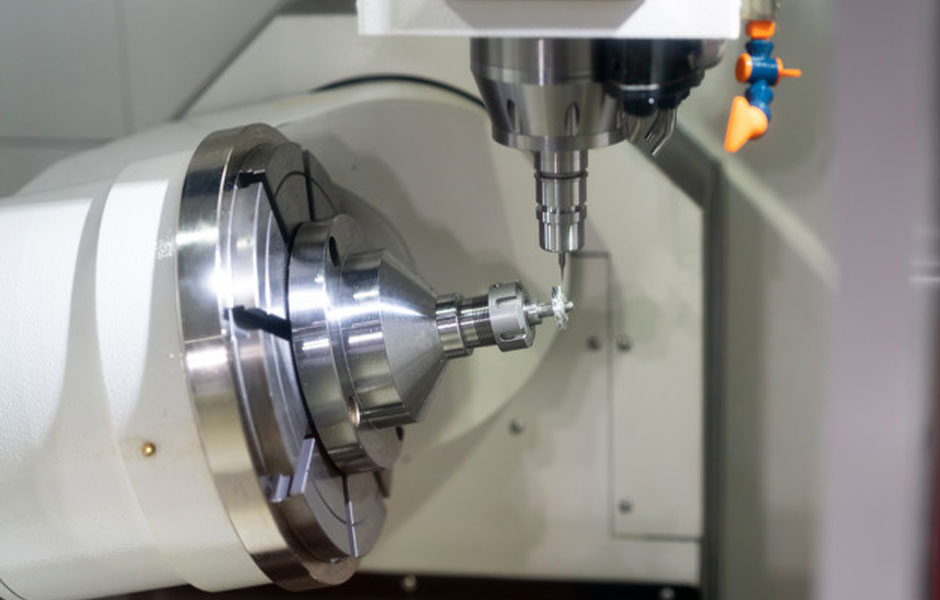
5 Axis machining is a mode of CNC machining. The machining centers we usually use now are generally three-axis three-linked machining centers. Three-axis refer to the X, Y, and Z axes of the machining center. Of course, there are 4 axis machining centers. 4-axis machining centers refer to the X-axis, Y-axis, Z-axis, and A-axis. Here, the A-axis refers to the axis that rotates around the X-axis. The five-axis machining center refers to the B axis in addition to the X, Y, and Z axes, and the B axis refers to a rotation axis around the Y axis. This technology has been widely used in high-precision instrument manufacturing fields such as ships, aerospace, automobiles, the light industry, and medical treatment.
3 axis machining centers and vertical machining centers are commonly used in traditional mold processing to complete the milling of workpieces. With the development of mold manufacturing and processing technology, the ball-end milling cutter commonly used in traditional mold processing has obvious benefits, but if it is applied to vertical machining centers, the bottom surface speed is zero, and the finish is poor, so the weaknesses of traditional mold processing gradually appear. The 5-axis machining can process different sides of the workpiece without changing the position of the workpiece on the machine tool, which can greatly improve the processing efficiency of prismatic parts.
What are the advantages of 5-axis machining
- Reduce Machining Time
In five-axis machining, flat-bottomed end mills are used to maintain a vertical state of the complex mold processing surface, which can greatly reduce the processing time. The principle of the five-axis machining center is also suitable for side milling with angled surfaces, which can eliminate rib-like lines caused by ball-end milling, making the surface quality of the mold more ideal, and reducing the need for cleaning the mold surface The workload of manual milling and manual work.
- Improve Machining Accuracy
Through the five-axis machining technology, the problem that the workpiece needs to be repositioned at a complex angle and needs to be debugged multiple times is solved, which not only shortens the time but also greatly reduces the error generated. The tooling fixture required when installing the workpiece A large amount of cost has also been saved, and the machine tool has also achieved the processing of complex parts, such as the drilling, taper processing, and cavity recesses required for complex surfaces, which are not possible with traditional methods.
- High Production Efficiency
The five-axis machining center can effectively reduce the machining time and auxiliary time of the parts. The five-axis linkage machining center has a large range of spindle speed and feed, allowing the machine tool to perform powerful cutting with a large amount of cutting. The five-axis linkage machining center is currently entering In the era of high-speed machining, the rapid movement and positioning of moving parts of the five-axis machining center and high-speed cutting processing have reduced the turnaround time between semi-finished products and improved production efficiency.
5-axis machining gives designers a huge level of flexibility to design very complex 3D geometry. Understanding the possibilities of each type of CNC machining is essential in the design of CNC machined parts. If your design needs the use of a 5-axis CNC, make the most of it!
CNC Machining Service
DFM Rapid is a CNC manufacturing and sheet metal fabrication company, including CNC machining services, CNC milling services, CNC turning services, laser cutting services, and stamping services.
DFM Rapid offers professional CNC machining and rapid prototyping service for making a wide array of product parts. Our excellent quality control systems ensure that all our deliveries are speedy and standard for every manufacturing size in both low-volume and high-volume productions. Feel free to reach out for a free quote on your project