Computer Numerical Control (CNC) machining remains one of the most diverse manufacturing processes in the industry today. With computer-aided control, manufacturers can affordably produce high-precision end-use parts with complex geometries. In CNC machining, whether you want to create a single prototype or go into mass production, the main priority is often to reduce manufacturing costs. Fortunately, design decisions can help keep the price down. By simply following the design of the machinability rules, you can manufacture affordable parts that still meet functional design requirements.
What affects the cost of CNC parts?
The price of CNC machined parts depends on the following:
- Machining time: The longer it takes to machine a part, the higher the cost. Machining time is often the main cost driver for CNC.
- Start-up costs: These relate to CAD file preparation and process planning, and are significant for low-volume production. This cost is fixed and there is an opportunity to reduce unit price by exploiting “economies of scale”.
- Material Cost: The cost of bulk material and the ease with which that material can be machined greatly affects the overall cost of a CNC. Optimizing your design while considering certain materials can significantly reduce the price.
- Other manufacturing costs: When you design a part with special requirements (for example, when you define tight tolerances or design thin walls), special tooling, tighter quality control, and more machining steps may be required—in more at low processing speeds. Of course, this has an impact on the total service and manufacturing time (and price) of the CNC.
Here are tips to help you design more cost-effective machined parts
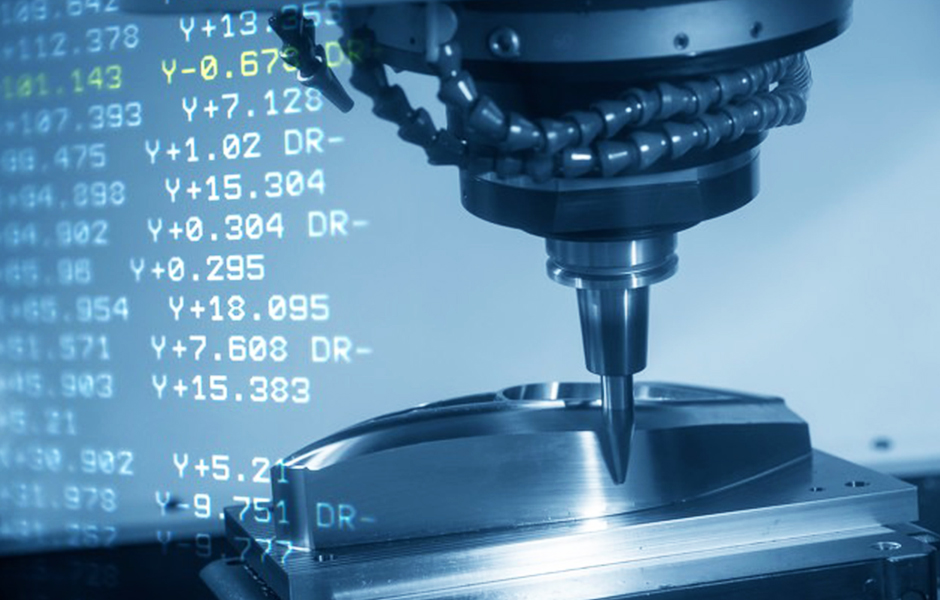
Use Cheaper Materials
Expensive doesn’t always mean better. Raw materials play a huge role in the inflation of production costs. Choosing materials wisely can save a lot. We don’t ask you to compromise on quality in any way; in fact, using cheap, substandard materials often results in unexpected expenses.
Eliminate vertical edges and sharp corners
CNC machines, by default, machine many cylindrical parts. Because of this, every groove, hole, and channel that a machine cuts usually has this circular geometry. Therefore, designing parts with sharp corners is very difficult when using CNC machining techniques. Although not impossible, making parts with sharp corners and vertical edges on a CNC machine will require more effort. If possible, remove sharp vertical edges and corners. You can also reduce the cost of CNC parts by maximizing the radius of each corner to allow larger tools to remove material more efficiently, reducing production time.
Avoid Deep Pockets
Deep pockets can negatively impact the cost of CNC machining, as achieving deep pockets means removing a lot of material. Removing material is time-consuming and may require the use of special tools to achieve your desired depth. Try to limit the pocket depth in your design to four times the length. CNC tools do have limitations when it comes to grooving – ideally, two to three times as deep as their diameter. Up to four times the diameter can be cut, but this will cost you more money.
Split Complex Parts
If you have a complex part—such as a complex geometry that requires rotation or repositioning—machining your part may involve custom fixtures, manual rotation, repositioning, or a multi-axis CNC system. All of this comes at a price. If you can’t reduce the complexity of the part, you can still reduce CNC machining costs by splitting the part into two or more separately machined parts that can be assembled into the parts you need. By breaking a part into two or more geometries that can be machined in a single setup, you may find cost reductions.
Specify Tolerances Only For Critical Features
Specifications are critical for precision CNC machining. Entrepreneurs usually define what they want and what they want. But part design—especially tighter tolerances—has a huge impact on production costs. We recommend that you keep standard tolerances for general characteristics. If absolutely necessary, you can specify tolerances for certain key characteristics and functions.
Reinforced Threaded Holes
If your part requires threaded holes, there are two main factors that add to the cost: hole depth and thread size. Contrary to popular belief, increasing the length of the thread in the hole does not hold the bolt any tighter. In reality, it’s just the first two or three rounds that do most of the work. With that in mind, you probably don’t need a hole that’s threaded more than three times the hole diameter. Going deeper than this will inevitably increase the likelihood of tap breakage and increase the time of the tapping operation.
Avoid multiple completions
Applying surface treatments such as reduced surface roughness, knurling and other textures at the machining stage can increase cycle times. Post-processing finishes such as anodizing, chemical conversion coatings or paints are applied after the part has been machined. Each completion requires setup and potential masking. For multiple surface treatments, such as chemical conversion and anodizing on the same part, additional processing steps are required, adding time and cost to each part.
Order More Quantity
Granted, modern CNC machines can combine multiple operations to operate more efficiently, however, they still require programming and setup. Ordering multiple quantities of the same part can help increase productivity and reduce cost per piece. During the production phase (up to 10,000 parts) CNC machining offers the greatest cost-effectiveness.
For Reliable And Effective CNC Machining Services, Contact Us
If you are looking for CNC machining Services for your next project, please feel free to get a quote.